The 40mm Bofors has become the quintessential anti-aircraft artillery piece of WWII — perhaps of the 20th century. The 40mm Bofors was developed in Sweden beginning in 1929, and by 1932 the design had been perfected. After firing a 1.96-lb shell to a vertical range of 4.3 miles with at an average rate of 80-100 rounds per minute in the Spanish Civil War, the weapon drew the attention of armed forces world-wide.
Accordingly, the U.S. Army in May 1937 sought to obtain a test gun from Aktiebolaget Bofors (AB Bofors). The reply from the firm read in part, “…we are unfortunately not in a position to provide…the materiel asked for, as we on principle do not sell guns and ammunition for demonstration purposes.”
However, the Chief of the Coast Artillery, Major A. H. Sunderland, who at that time was responsible for antiaircaft weapons for the US Army, remained interested, and wrote that “…efforts to determine the suitability of the Bofors 40mm gun should be continued with renewed vigor,” and suggested that Ordnance officers be sent to the Swedish plant to witness a demonstration of the equipment. Captain R. R. Studler, Assistant Military Attache, London, and Major Gordon B. Welch were given the assignment and made their report after witnessing the demonstrations Aug. 18 and 20, 1937.
Based on their report, on Dec. 6 the U.S. government requested quotations from Bofors for supplying guns and ammunition. The firm replied on Dec. 22 that delivery of such material would require at least two years lead time, however, they would be willing to license production.
Chief of Ordnance Major General C. M. Wesson, was having none of this, opting instead for the U.S.-designed 37mm antiaircraft gun, and apparently persuaded Coast Artillery to change their mind, writing on Feb. 4, 1938 that, “In view of the fact the procurement of intermediate caliber weapons from foreign sources is not favorably considered by the War Department, which is now concurred in by the Chief of Coast Artillery, this office recommends that no further negotiations be carried on with the Bofors company looking toward the procurement of materiel discussed herein.” This decision would ultimately delay U.S. use of the Bofors by two years.
Across the Atlantic, the British Army began testing the weapon in 1937 and found it to be superior to other weapons. A license to manufacture the weapon was acquired from Bofors, and teams of engineers set out to convert the weapon’s engineering from Metric to Imperial measurements. At the same time, efforts were made to speed production. Bofors had envisioned that each weapon would be hand-assembled — whereas the wartime climate in Britain demanded mass production. Ultimately, the gun became standardized as the QF (Quick Fire) 40mm Mark III.
In September, 1939, the Swedish Legation, acting on behalf of the Bofors company, approached the York Safe and Lock Company, asking if the firm would consider manufacturing the guns in the U.S. in accordance with the drawings of the AB Bofors. York in turn asked the Chief of Ordnance if this would bring legal difficulties, to which the reply came there would be no objection so long as such work did not interfere with the firms work for Ordnance. Despite this response, no agreement was made with Bofors at that time, although at a later date York did build guns for the Navy.
In the interim, the Bofors came to the attention of the U.S. Navy Bureau of Ordnance, which purchased a twin mount weapon directly from Bofors in August 1940. This mount was delivered in October and demonstrated to both US Navy and Army personnel on Oct. 15 at Dahlgren Proving Ground, Va. The superiority of the gun was obvious, and while negotiating for manufacturing rights with Bofors, the Navy also obtained drawings of the gun as well as Dutch fire control equipment from the Dutch. The story of these drawings has been subject to considerable lore, but Chief of Ordnance history of the Bofors states the following:
“Admiral Blandy (then Captain) had been told by a Dutch admiral of the excellence of the Dutch fire control equipment and it was suggested that he might wish to see it in action on a Dutch ship soon to make the West Indies. Admiral Blandy went down with an American cruiser which could launch planes to tow targets, and was so impressed with the firing data that he arranged to have the drawings microfilmed at Surabaya, Java, and flown to this country. (Such drawings were not available from Holland as that country had already been overrun by the Germans.)”
Rear Admiral W. H. P, Blandy stated that the story that these drawings were flown out of the Dutch East Indies barely in time to escape the oncoming Japanese is apocryphal — “a lovely story, but untrue.”
Essentially overriding Wesson’s earlier directive, on Sept. 2 1940, the Army’s Chief of Staff, General George C. Marshall, wrote to Sir Henry Tizard, Chief of the British Technical Mission, asking for a battery of four British-built Bofors gun and fire control equipment. Tizard replied that it was unlikely that Britain could release so much equipment, but arranged to have one complete gun shipped to Aberdeen, where it arrived on Nov. 19, 1940, where a British crew demonstrated the weapon on Nov. 25.
While the U.S. Army was waffling about the Bofors design, the British were not, and desperately needed more of the guns. On Jan. 2, 1941, the War Department decided to permit the British to order 40mm Bofors guns from U.S. manufacturers, “…with the proviso that this will not establish a precedent for the substitution of other non-standard items in the British “B” program.”
Additionally, that same month the Navy informed the Army that the Navy had been able to negotiate for a license to produce the weapons, with the War Department recording the details as “First, the Bofors company reduced their price to a flat $600,000 for license to manufacture the naval mount, an Army mobile AA gun and carriage (the latter as covered by U.S. patent No. 2,103,670) and ammunition for both these guns. Blueprints, manufacturing drawings, and the services for one year of two production experts were also to be supplied. Secondly, the Army agreed, on 4 June 1941 to pay half the cost of this license, or a total of $300,000.”
A contract was signed with Bofors on June 21, 1941 by the Navy providing that in consideration of the sum of $600,000, an “Exclusive and irrevocable license to make, use and have made in the United States for the United States use” the Bofors 40mm water-cooled gun for naval use, the Bofors 40mm air-cooled gun for army use, all types of ammunition therefor, and the Bofors field carriage for 40mm guns.”
The money was paid, and Bofors delivered to the Naval Attache at the American Legation in Stockholm all plans, specifications, manufacturing drawings and engineering data necessary to enable our people to manufacture guns and ammunition under the Bofors secret process.
The Ordnance Committee Minutes (OCM) Item 16448 of Feb. 6, 1941 designated the gun as Standard T1, with carriage T1. Those designations were both changed to M1 by OCM 16647 on April 9, 1941, which also provided that the Bofors would definitely replace the 37mm antiaircraft gun.
Two pilot weapons were ordered from Chrysler on Feb. 3, 1940, and the company asked to prepare detailed drawings based on a British-built gun sent to them for study, as well as drawings, also furnished by the British. Ultimately, for the work on this contract, number W-374-ORD-1170, the government paid $87,223 for the two pilot guns, less barrels, and the drawings.
Firestone Tire and Rubber Company was simultaneously issued a similar contract, number W-303-ORD-917, with respect to two pilot carriages and associated drawings, in the amount of $69,960.
On April 16, 1941, the Navy issued a Letter of Intent with Chrysler calling for the tooling up for production of 500 40mm Bofors guns per month. The month prior, the Army had ordered from Firestone 1,000 carriages, which later rolled into contracts W-303-Ord-952 and DA-W-303-Ord-8, for a total of 2,236 carriages, the first of which was delivered in February 1942. A similar number of guns were ordered from Chrysler, with 4,472 gun barrels ordered from Otis-Fensom in Canada on contract DA-W-374-Ord-5 and W-374-Ord-1141.
The pilot guns and carriages were proof tested on July 2, 1941.
In October 1941 the M2 carriage was introduced, which reflected the difference between the M1 British-designed carriage, and the American carriage, which used an American-type drawbar and lunette, electric brakes, and M5 remote control system utilizing 60-cycle current in lieu of the 50-cycle current used on the British M3 control system.
Beyond the above, and somewhat more complex, was the subject of rifling the barrels. The barrels for the U.S. pilots used the Otis barrel tubes, but were rifled by Watervliet Arsenal at a uniform twist of one turn in .30 calibers, whereas the original Bofors rifling, as well as that of the British, was an accelerating rifling, beginning at one turn at .45 calibers at the breech and increasing to one turn in .30 calibers at the muzzle. The constant rate of rifling was obviously easier to manufacture, and it was believed that this would produce a satisfactory weapon.
However, testing of the pilots in December 1941 and April 1942 revealed that tube with increasing twist (the Bofors design), had an accuracy life of 6,000 rounds, vs 4,200 rounds for the American uniform one turn in .30 calibers rifling. Further, the original barrel design resulted in improved accuracy and also lessened the strain on the bun and mount. Thus, the decision was made to produce barrels in accordance to the rifling specified by Bofors.
The sighting and fire control equipment consist (late 1943) of Bofors direct fire sights on the carriage; and, off the carriage, director M5A1, remote control system M10, generating unit M10, and gunner’s quadrant M1 or M1918. The elevating and traversing mechanisms are provided with individual electro-oil drives operated by 0.6-hp electric motors. In the event of failure of the remote control system, power plant, or director, the direct sighting system is used. The firing mechanism can be operated either by front or rear foot pedals interconnected and linked to the firing lever. The gun can, of course, be placed on safety, and can be adjusted for single shot or automatic fire.
For the British, the M1 gun and the less-rugged British-specified M1 carriage were made. That first order for 2,236 complete guns and carriages, mentioned above, was actually for the British on a Lend-Lease basis. The record shows, however, that this order was cut back to 1,500 units, and of those the British got only 1,392 of them. These 1,500 were the total U.S. M1 carriage production.
Gun mechanisms, as made by Chrysler, were also supplied to the British for mounting on ships on mounts of their own make. The United States Navy, having financed Chrysler’s new 40mm plant, as of 1944 had taken about 15 percent of the corporation’s production of gun mechanisms — those being water-cooled, as opposed to the Army’s air-cooled guns.
Although there was considerable procrastination and delay on the part of the U.S. to initiate production of the Bofors, once the decision was made, the weapons moved rapidly into production — and the U.S. production was the first true mass production of the Bofors gun. Abroad, the guns were produced essentially by toolroom methods, as were the two U.S. pilots. Chrysler engineers revised the manufacturing process and product specifications to facilitate mass production. For example, previously, bar stock was specified for complex pieces, even though 90 percent of the metal was later machined away. Additionally, the flash hider was originally machined from a solid steel forging weighing 40 lbs., though the finished bell-mouthed assembly weighs 10 pounds. To simplify this, the Chrysler engineers tried pierced forgings, but while simpler, difficult machining was still necessary, and complicated fixtures and critical machine tools were required.
Next, the engineers tried a relatively simple swaging operation, in which one end of a tube is swaged down by a die ring and the other is flared by a punch. This method was a resounding success and was subsequently adopted. This and other simplifications of the design of the flash hider, many tons of steel are saved each month, six machines of a critical nature could be reassigned to other work, and nine machines, otherwise necessary when gun quotas were increased, were not ordered. Most significantly, something like 4,893 man-hours were saved by Chrysler alone in the manufacture of this single part.
Delivery of the first 25 guns had been scheduled for October 1941, but because of difficulties in obtaining the needed machine tools, the first delivery of 19 guns was not made until February, 1942. Production of gun mechanisms began Dec. 15, 1941; final assembly was begun on Jan. 5; and the first mechanism was completed Feb. 5, 1942.
Once started, Chrysler rapidly ramped up production, from the first 19 in February to 134, 379, 500, 692, 840, in the next five months respectively, and onward to a peak of 1,600 in December 1942. At the same time, Chrysler’s production of gun barrels began in March with an output of only four, but rose rapidly to 1,492 in June, before dropping to around a thousand for three months, then jumped up to 3,336 for November, and hit a new high of 4,199 in January, 1943. The stock for the barrels was supplied by Atlas Steel, Timken Ordnance Plant, and Watervliet Arsenal in the form of rough forged tubes, pierced upset tubes, and centrifugal cast tubes, by the three facilities, respectively.
Post Pearl Harbor demand for the guns increased, and to augment Chrysler’s production, a contract was issued to the Pontiac Motor Division of General Motors. The Pontiac contract was not as large as those issued to Chrysler, therefore no plant expansion was required. Bofors production required about a quarter-million square feet of Pontiac’s 3,400,000 square feet of floor space in the city from which it took its name.
Similarly, additional sources of supply for carriages were needed.
In October 1941, the first order for 750 carriages was given to The Koppers Company, whose commercial business was medium size forgings, bronze and iron castings, welded steel products, and machinery and weldments. Additional orders were given so that when Koppers’ contracts ware completed the company had made a total of 2,270 carriages.
Farm equipment manufacturer J. I. Case Company was awarded a contract for 2,000 carriages in March 1942. The first deliveries were scheduled for September and were actually made in October. At the end of 1943, the company had completed its schedule, having made only 1,414 carriages due to government cutbacks from the original order.
Firestone began production of a new model carriage on July 20, 1943: the M2A1. The M2A1 differed from the previous M2 in that its rate of traverse was increased about 70%, making it more capable of tracking the faster moving aircraft then prevalent. This change was formally authorized by OCM item 21098 the next month.
Twelve Chrysler plants, along with some 2,000 subcontractors, were involved in the weapon production. Ultimately, 30,095 air-cooled single guns and 14,442 twin guns were built, along with more than 120,000 barrels.
Chrysler’s impressive production was augmented by Pontiac Motor Division, which built in excess of 4,900 of the single guns.
By 1945, Allied air superiority, combined with the overwhelming production of the weapons to that stage in the war, meant that all U.S. Army requirements were satisfied. While additional guns were built in 1945, they were all for the Navy.
The U.S. Army employed its share of these new wonder weapons throughout WWII and beyond. As the U.S. entered WWII, anti-aircraft artillery was a branch of the Coast Artillery Corps. Antiaircraft artillery was not separated from the Coast Artillery until 1943. Typical organization during the coast artillery days involved three-battalion regiments consisting of a gun battalion, an automatic weapons battalion, and a searchlight battalion. In 1943, these regiments were broken down into separate battalions. These battalions were either gun battalions, with the M1 90mm anti aircraft cannon, or an automatic weapon battalion. The automatic weapons battalions were at first armed with the M1 37mm AA gun, but were later rearmed with the M1 40mm Bofors. In either event, the cannons were supplemented by quad-mount .50 caliber machine guns.
Each of the automatic weapons battalions consisted of four firing batteries, lettered A to D, an H&H Battery, and a Service Battery. In most instances, each battery was comprised of eight towed M1 40mm cannon (or M1 37mm) divided into two platoons and eight quad-mount .50 caliber machine guns, also in two platoons. Mobile batteries had the quad mount on trailers, while self-propelled batteries had the machine guns mounted in half-tracks. Typically, an automatic AAA weapons battalion was attached to each division. Armored divisions got self-propelled AAA battalions, and infantry divisions got mobile AAA battalions. Corps had attached to them a AAA group, consisting of two or more automatic weapons battalions. Armies and theater commands were assigned AAA brigades.
Increasing speeds and altitudes of aircraft began to render the Bofors guns obsolete by the late 1940s, and newer weaponry replaced them in most fronts. But even today the Bofors can be found soldiering on in AC-130 aircraft and small surface ships, only a lack of spares and ammunition forcing their withdrawal.
An important detail of the license between the Navy and AB Bofors was the “for the United States use” clause.
The United States immediately began to product the guns and also to transfer, under the Lend Lease Act and similar legislation, Bofors guns and ammunition to other nations to be used by them in the common war against Germany and Japan.
Bofors regarded such transfers as beyond the scope of the license which it had granted, and protested vigorously. Beginning in 1941 and continuing throughout several succeeding years, it informally asked the American authorities either to work out a royalty arrangement for the unlicensed use of the trade secret, or to submit its claim for extra compensation to arbitration as provided in the contract. When all efforts to obtain an equitable adjustment through informal negotiation proved fruitless, on May 23,1947 Bofors addressed to the Secretaries of State, Defense, Army and Navy a formal document styled “Petition for Agency Action.” It contained a full statement of the facts and again requested that those officials agree either to grant compensation for unauthorized use of the trade secret or to submit the dispute to arbitration.
The petition for agency action was rejected by all four Secretaries, after which Bofors filed three lawsuits against the United States government in April 1950, and a further action on May 15, 1953. On July 12, 1957, the United States Court of Federal Claims ruled in favor of Bofors.
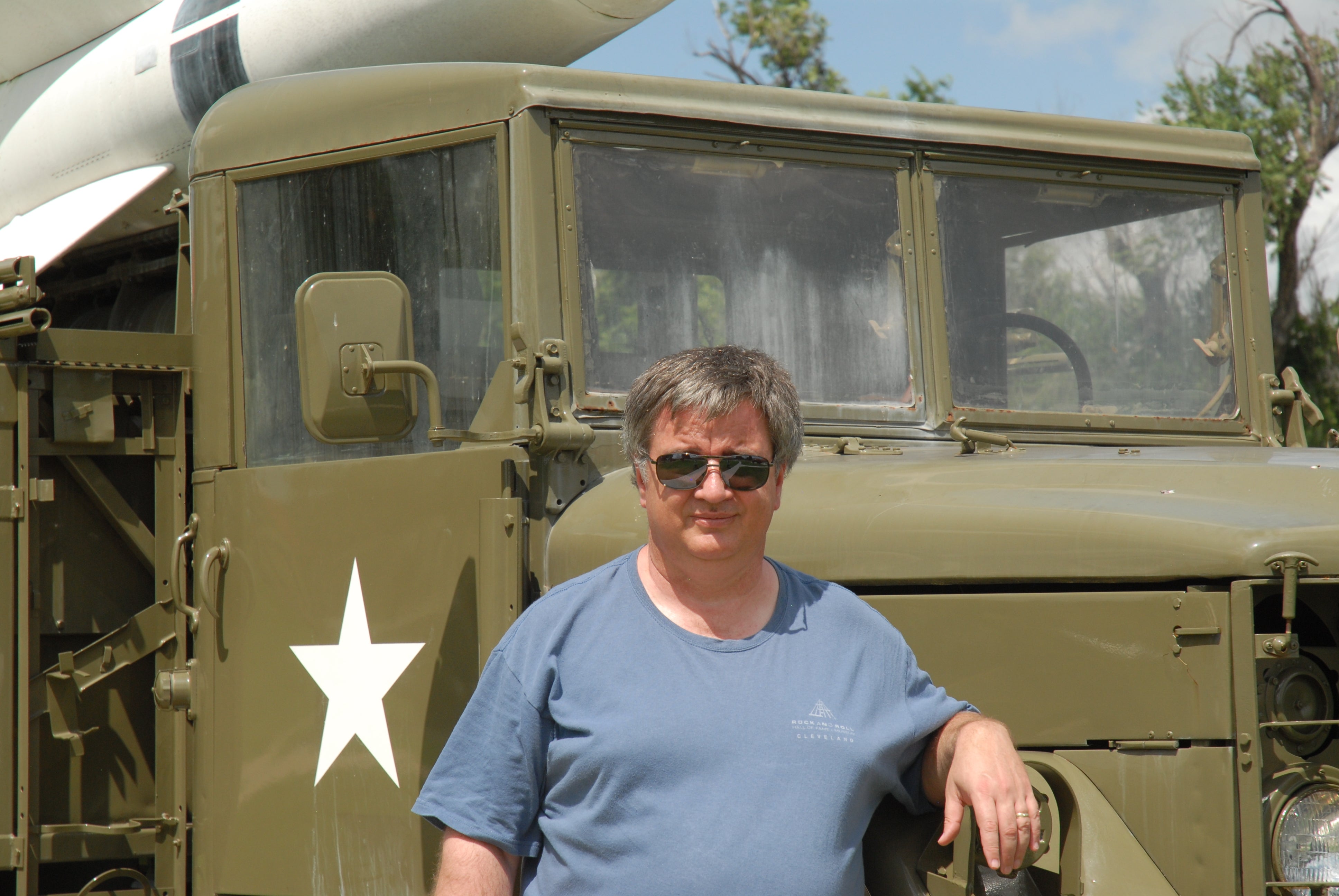
David Doyle's earliest published works were occasional articles in enthusiast publications aimed at the historic military vehicle restoration hobby. This was a natural outlet for a guy whose collection includes several Vietnam-era vehicles such as M62, M123A1C, M35A2, M36A2C, M292A2, M756, and an M764.
By 1999, his writing efforts grew to include regular features in leading periodicals devoted to the hobby both domestically and internationally, appearing regularly in US, English and Polish publications.
In 2003, David received his a commission to write his first book, The Standard Catalog of U.S. Military Vehicles. Since then, several outlets have published more than 100 of his works. While most of these concern historic military hardware, including aircraft and warships, his volumes on military vehicles, meticulously researched by David and his wife Denise, remain the genre for which he is most recognized. This recognition earned life-time achievement in June 2015, when he was presented Military Vehicle Preservation Association (MVPA) bestowed on him the coveted Bart Vanderveen Award in recognition of “...the individual who has contributed the most to the historic preservation of military vehicles worldwide.”
In addition to all of publishing efforts, David is the editor of the MVPA’s magazine, History in Motion, as well as serving as the organization’s Publications Director. He also maintains a retail outlet for his books online and at shows around the U.S.